本文详细阐述了产能利用率的计算方法,并分析了影响产能利用率的多种因素,包括内部因素如技术水平、管理效率和员工素质,以及外部因素如市场需求、原材料供应和政策法规。文章还探讨了不同行业产能利用率计算的差异,以及如何通过改进产能利用率来提升企业效益。文中结合实际案例,深入浅出地讲解了如何计算产能利用率以及如何提高产能利用率,为企业管理者提供有益参考。
产能利用率的基本计算方法
产能利用率是指企业在一定时期内实际产出量与最大生产能力之间的比率,反映了企业生产能力的利用程度。其计算公式通常为:产能利用率 = (实际产出量 / 最大生产能力)×100%。
例如,一家服装厂设计最大产能为每月生产10000件衣服,但实际生产8000件,那么该厂的产能利用率为:(8000 / 10000)×100% = 80%。看起来简单明了,但实际操作中,我们需要明确几个关键点:首先,实际产出量应是合格产品数量,而非包含次品或废品的总产量。其次,最大生产能力并非一成不变,它会受到设备状况、员工熟练程度、市场需求等多种因素的影响,需要根据实际情况进行动态调整。
一些企业在计算产能利用率时,会根据自身情况调整计算公式。例如,某些企业可能更关注产能利用率的稳定性,会采用更复杂的加权平均方法计算。也有企业会在计算中加入一些调整系数,来更准确地反映实际情况。
准确地计算产能利用率,对企业进行生产计划、成本控制、资源配置至关重要。一个高的产能利用率通常意味着高效的资源利用和较高的盈利能力,反之则可能存在生产效率低下或资源浪费等问题。
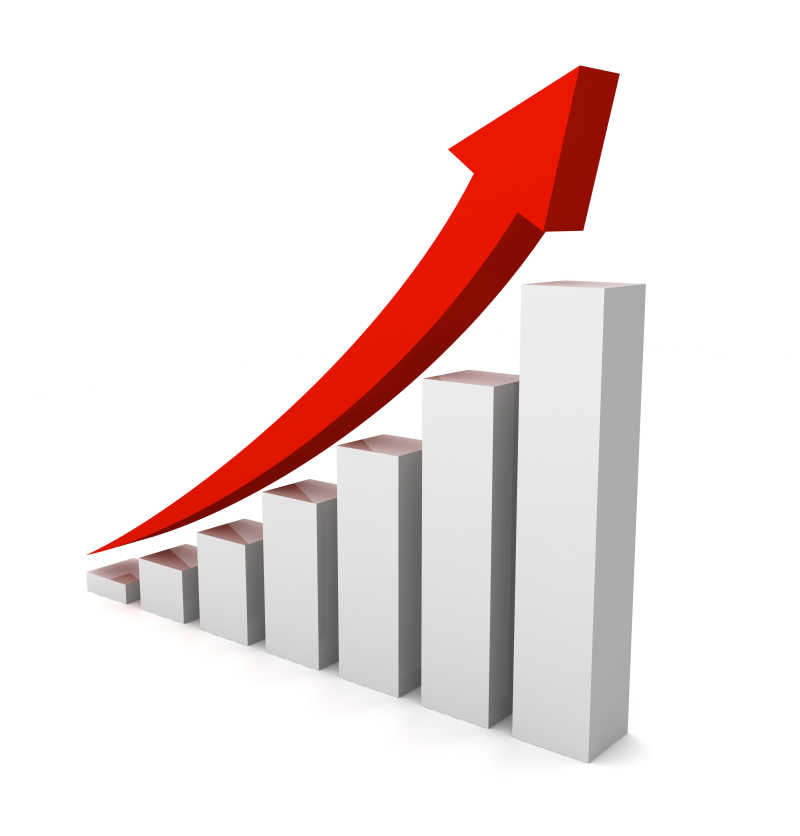
影响产能利用率的因素分析
影响产能利用率的因素错综复杂,既有内部因素,也有外部因素。内部因素主要包括技术水平、管理效率、员工素质等。技术水平高的企业,通常拥有更先进的设备和更成熟的工艺,生产效率自然更高,产能利用率也更容易提升。管理效率高的企业,能有效组织生产,减少资源浪费,提高产能利用率。员工素质高,工作效率高,出错率低,自然也能提高产能利用率。
外部因素主要包括市场需求、原材料供应、政策法规等。市场需求旺盛时,企业订单多,产能利用率自然较高;反之,则可能导致产能利用率下降。原材料供应不足或价格上涨,也会影响企业的生产计划,降低产能利用率。政府的政策法规,例如环保政策,也会影响企业的生产活动,从而影响产能利用率。
理解这些因素,对于企业提升产能利用率至关重要。企业需要不断提升自身的技术水平、管理效率和员工素质,同时密切关注市场需求变化,加强与供应商的合作,积极应对外部环境的变化。
不同行业产能利用率的计算差异
产能利用率的计算方法虽然基本一致,但在不同行业中,其具体应用和侧重点却存在差异。
例如,制造业通常关注设备的利用率和生产线的效率,计算时会更侧重于机器运行时间和产品产量。而服务业则更加关注人力资源的利用效率和服务质量,产能利用率的计算会更注重服务人员的服务时间和客户满意度。
此外,不同行业的产能利用率的衡量标准也可能不同。例如,在重工业中,产能利用率可能以吨位或立方米为单位进行计算;而在轻工业或服务业中,则可能以件数或人次为单位进行计算。
因此,企业在计算产能利用率时,必须结合自身行业特点,选择合适的计算方法和衡量标准,才能更准确地反映企业的实际生产能力和效率。
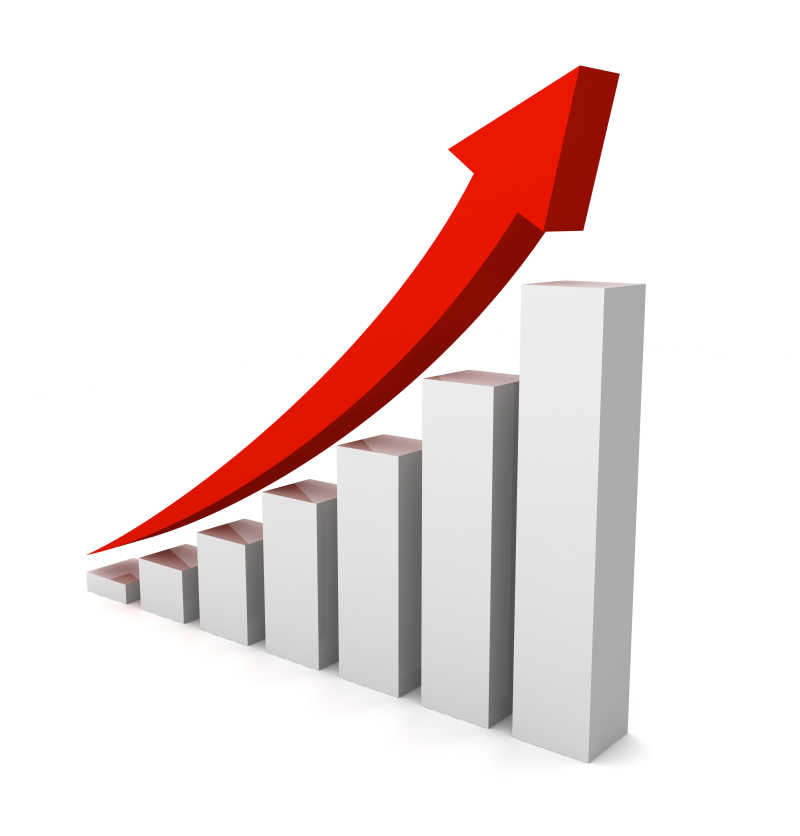
产能利用率的应用与改进
- 通过产能利用率数据,企业可以及时了解生产效率,发现问题并及时调整生产计划。
- 利用产能利用率数据,可以更好地进行成本控制,避免资源浪费。
- 提高产能利用率可以提升企业效益,增加盈利。
- 根据产能利用率数据,可以进行科学的设备维护和保养,延长设备寿命。
- 根据产能利用率数据,可以对员工进行更有效的培训,提高工作效率。